DE L’IDÉE A LA PREUVE DE CONCEPT – UN PARCOURS AU CŒUR DE L’INNOVATION
Publié par Arche Aux Innovateurs Kahloïdoscope, le 17 avril 2024 770
La genèse du projet de cette équipe 51, l’équipe Kahloïdoscope, trouve ses racines dans le serious game de l’Arche aux Innovateurs, parcours de formation d’éco-innovation collective. Le défi : trouver un produit si possible novateur, du moins suffisamment original, différenciant et réalisable au Fab Lab de la Casemate à Grenoble. Ce parcours de 6 semaines nécessite de passer par toutes les étapes de la création d’entreprise, de la naissance de l’idée au business plan, et du prototypage de notre produit jusqu’au pitch final, en passant par bien d’autres étapes.
Après un brainstorming intensif, l’élimination d’idées lumineuses et de nombreux rebondissements liés à la dure réalité du marché, le couperet tombe : nous incarnerons finalement une équipe d'innovateurs qui développe des montures de lunettes innovantes, flexibles, résistantes et durables, en impression 3D. L'éco-responsabilité est au cœur de notre projet.
Notre équipe se nomme “Kahloïdoscope”, contraction de “Kahlo” et de “kaléidoscope” :
- “Kahlo” en référence à la peintre Frida Kahlo, pour la touche de couleurs et de créativité,
- “kaléidoscope”, bel objet optique, qui à partir de divers éléments géométriques de formes et de couleurs différentes, génère à l’infini de nouvelles créations colorées et harmonieuses… à l’image de notre équipe, composée de personnalités issues d’horizons très différents, mais possédant des compétences et savoir-faire complémentaires, avec pour point commun la motivation et la volonté de mener ce projet vers le succès !
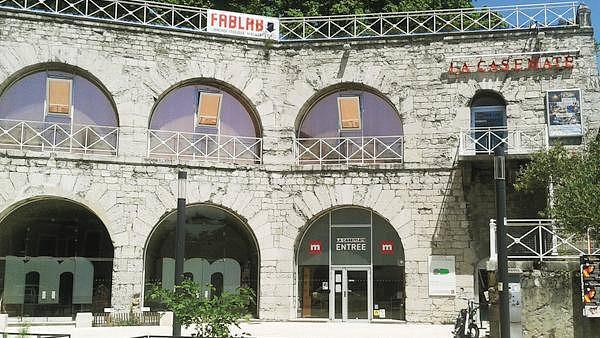
Dans le cadre de l’Arche aux Innovateurs, nous avons la chance de pouvoir nous initier aux différentes technologies proposées par le Fab Lab de la Casemate, Territoire de Sciences, le Centre de Culture Scientifique Technique et Industrielle (CCSTI) de Grenoble. Plusieurs matinées dans les ateliers vont nous permettre de prendre en main les logiciels et les machines afin de fabriquer des prototypes de nos montures. Notre équipe est pleine d'enthousiasme à l'idée d'acquérir de nouvelles compétences et de s'investir dans cet espace propice à l'innovation et à la création de projets novateurs. Animés par la volonté d'apprendre et de maîtriser de nouveaux outils, nous sommes impatients de contribuer activement à l'élan d'innovation qui caractérise le CCSTI de Grenoble.
LE PROJET : LES MONTURES DE LUNETTES FLEXIBLES
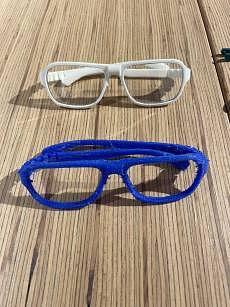
Notre idée : grâce à sa technologie unique, Kahloïdoscope propose des montures innovantes en impression 3D, flexibles, robustes et écoresponsables, sans compromis sur le confort.
Avant de pouvoir concrétiser notre idée, nous passons deux matinées à définir notre monture et à préparer les ébauches avant de concevoir les fichiers .stl finaux pour l’impression au Fab Lab.
Pour pouvoir tester la faisabilité technique du projet, nous décidons de partir sur plusieurs concepts à imprimer en 3D. Ceci nous permettra de tester :
- la monture monobloc
- la monture avec branches articulées
- divers types de matières, plus ou moins flexibles
- les adaptations nécessaires pour répondre aux besoins fonctionnels identifiés
Enfin nous y voilà : la réalisation de nos montures au CCSTI de la Casemate. En premier lieu, nous listons et estimons le temps que prendrait chaque tâche menant à bien la phase prototypage que nous souhaitons entamer, à savoir : une monture monobloc, une autre avec branches clipsables, un étui à lunettes ainsi qu’une simulation de verres optiques.
Pour cela, nous commençons à mettre en place les connaissances acquises au cours des semaines précédentes afin de lancer nos premiers tests en impression 3D et découpe/gravure laser. Suite à cette première séance de production, nous identifions déjà des déconvenues qu’il nous faut prendre en compte afin de lancer de nouveaux tests répondant davantage aux critères initiaux que nous nous sommes fixés.
Une équipe se positionne sur les ordinateurs pour préparer des fichiers sur le slicer (logiciel de découpe de l’objet en tranches) afin de lancer l’impression 3D.
C’est parti pour presque 3h d’impression : une monture monobloc en Flex bleu très souple, une autre en Flex blanc un peu plus rigide, et une monture avec branches clipsables sur la façade en PLA. L’imprimante Flex s’arrête au bout de quelques dizaines de minutes pour un problème de ventilateur : nous expérimentons l’importance d’être présent lors de la première heure d’impression pour pallier ces désagréments.
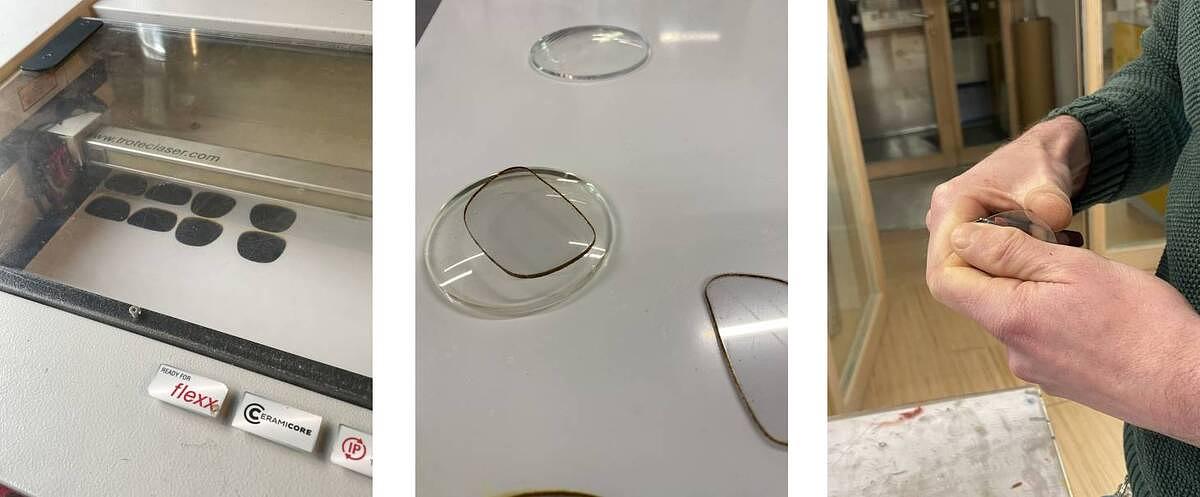
Une autre équipe a pris en main la découpe laser des verres en polycarbonate avant de poncer les bords et de tenter de les arrondir pour les rendre plus réalistes. C’est une véritable expérimentation qui s’opère : le matériau est chauffé à l’aide d’un décapeur thermique et posé sur un gabarit récupéré chez un opticien. La maîtrise de la température est tout un art : en effet, si le décapeur n’est pas assez chaud, le polycarbonate ne se déforme pas, mais s’il est trop chaud il commence à buller. La température idéale : 430°, pas plus, pas moins !
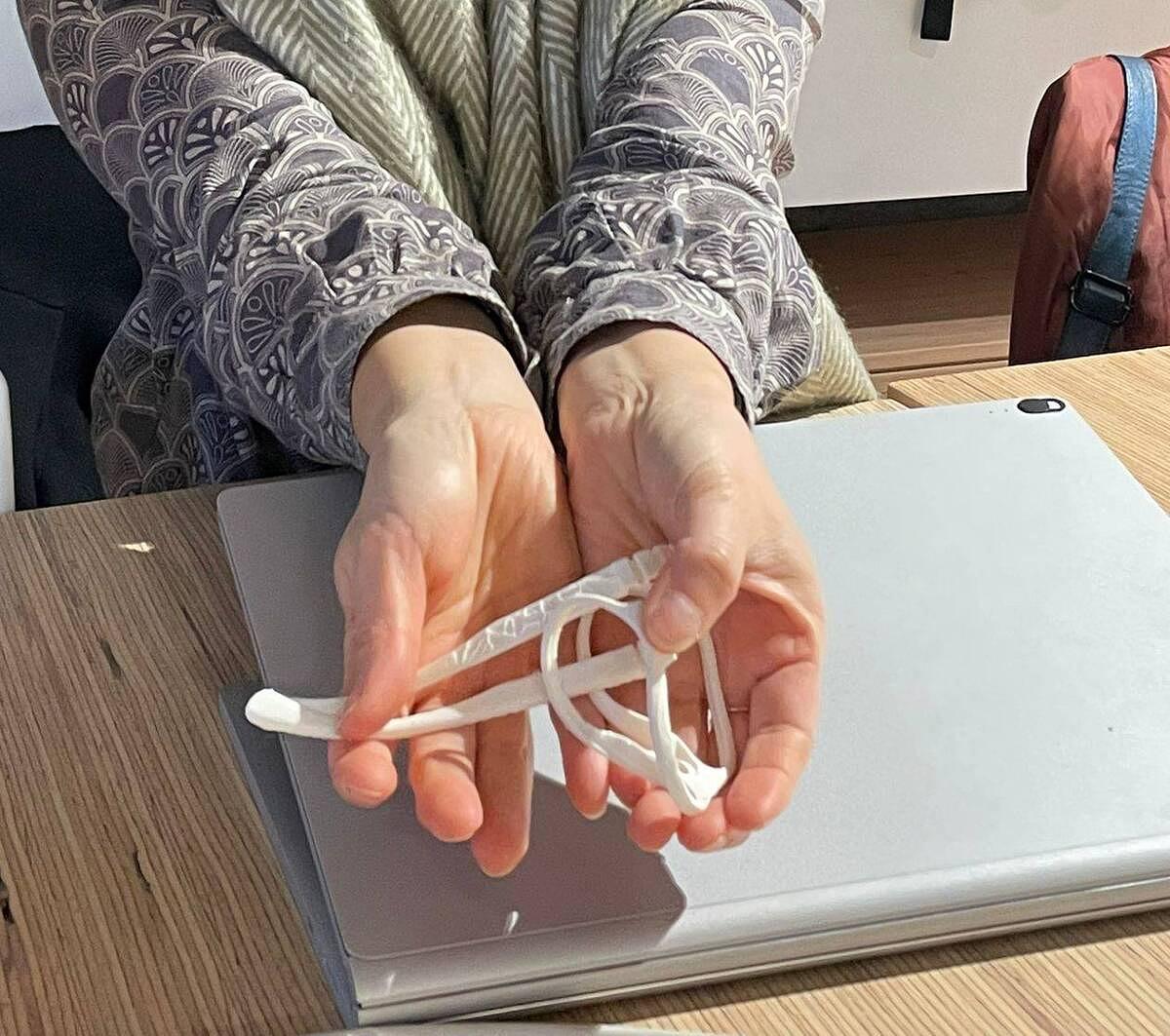
Nous avons en main, ou plutôt sur le bout du nez, nos premiers prototypes. Nous sommes fiers car nous avons réussi à prototyper les montures que nous avions imaginées : l’aboutissement d’un beau travail d’équipe ! Néanmoins, la qualité n’est pas forcément celle escomptée :
- les lunettes monobloc bleues sont trop souples et le rendu “effiloché” est médiocre : nous abandonnons ce matériau au profit de celui qui est plus rigide de couleur blanche, de meilleure qualité et que nous relancerons avec une meilleure définition d’impression,
- les branches clipsables ne se clipsent pas, ce qui est relativement fâcheux !
Néanmoins, c’est confiants et motivés que nous listons et nous répartissons les différentes tâches à effectuer pour lancer les nouveaux prototypes répondant davantage à nos attentes.
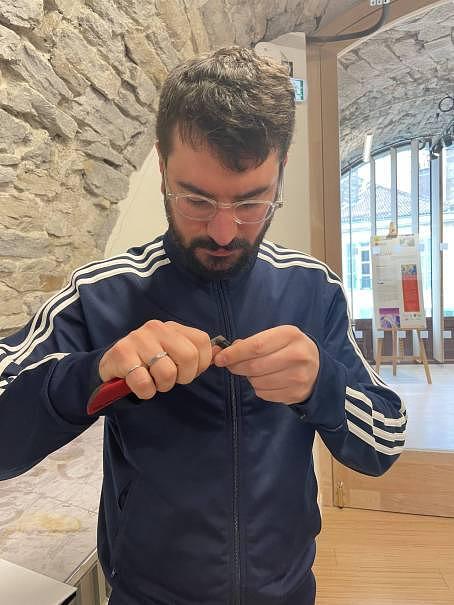
Une équipe, avec l'aide de Gaëtan, s’empare des branches pour mettre en œuvre les solutions envisagées : créer un sillon sur la façade ou poncer les “tétons” sur les charnières de branches afin de pouvoir les clipser sur la façade. Le sillon est difficile à creuser et cette idée est abandonnée. Le ponçage des saillies semble fonctionner et les branches se clipsent enfin à la façade. Nouvelle déconvenue : bien que clipsées à la monture, il est impossible de plier les branches !!! Un nouveau travail de fourmi nous attend : poncer, limer, enlever de la matière sur les branches afin de pouvoir les plier. Parallèlement, le fichier est retravaillé afin de pouvoir relancer une impression avec des branches adaptées.
Après un travail en équipe et plusieurs essais, les branches se plient enfin ! Notre monture est prête. Pas aussi souple et flexible que nous l’imaginions, mais robuste et éco-responsable.
Nouvelle utilisation du décapeur thermique afin de galber légèrement la façade… et nouvelle déconvenue : le plastique a trop chauffé et la façade s’est rétractée : les verres ne s’insèrent plus dedans ! Heureusement qu’une nouvelle façade est partie à l’impression 3D. Le galbage des branches se fera avec plus de précision et surtout une chaleur adaptée sur le décapeur thermique. Le résultat est assez bluffant : les lunettes tiennent parfaitement sur le visage.
Une autre équipe a relancé la découpe laser de nouveaux verres et leur ponçage. Le gabarit pour les galber n’ayant pas résisté au premier essai, nous décidons de ne pas former les verres et de les laisser plats dans les montures.
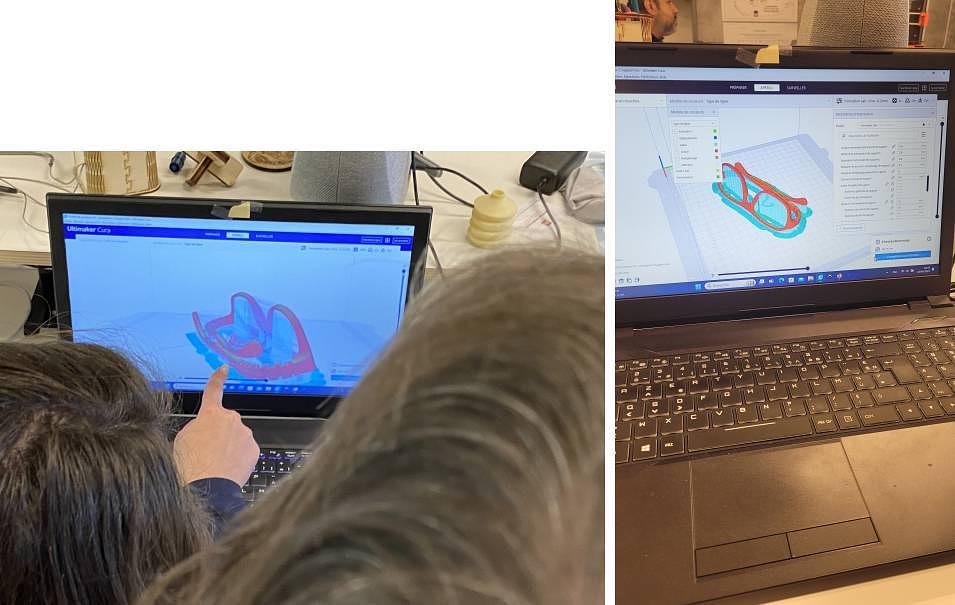
Une troisième équipe s’occupe de relancer l’impression de la façade de la monture avec les branches clipsables en Flexible TPU, un matériau plus souple, et de réimprimer la monture monobloc blanche en améliorant le rendu final.
Finalement, l’impression de la monture monobloc ne nous donne pas entière satisfaction car beaucoup de supports ont été nécessaires, ce qui engendre plus de déchets et soulève justement la question de la gestion des déchets inhérents à l’impression 3D quand cette dernière n’est pas optimisée. Le rendu n’est pas aussi net que nous ne l’imaginions.
Impression des branches à partir du fichier modifié. Insertion parfaite et repliage des branches sur la façade possible sans ponçage, limage ou autre expérimentation.
L’ETUI
Nos montures ont besoin de leur écrin : nous nous lançons dans la fabrication d’un étui en bois afin de pouvoir profiter des diverses possibilités de la découpeuse/graveuse laser.
Nous partons sur une boîte en contreplaqué de peuplier de 3 mm d’épaisseur.
Le premier prototype sort. Après l’étape d’assemblage, nous nous interrogeons sur la personnalisation de notre étui et décidons d’y graver notre logo.
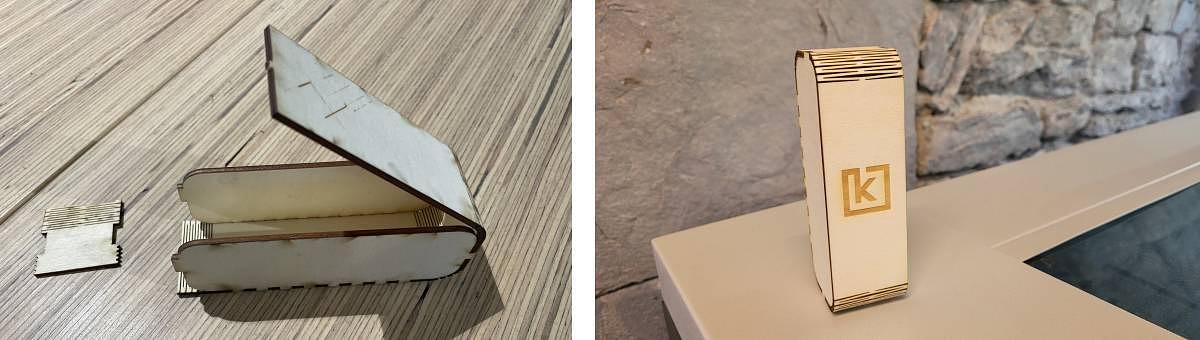
Un deuxième prototype est lancé avec la gravure. Nous sommes satisfaits du résultat. Néanmoins, l’étui ne fait pas l’unanimité : l’ouverture est délicate, il faut en coller une partie et l’étui en épaisseur 3 mm est fragile et l’ouverture casse. Nous décidons alors de passer à une épaisseur de 5mm pour solidifier l’étui et le rendre plus durable dans le temps.
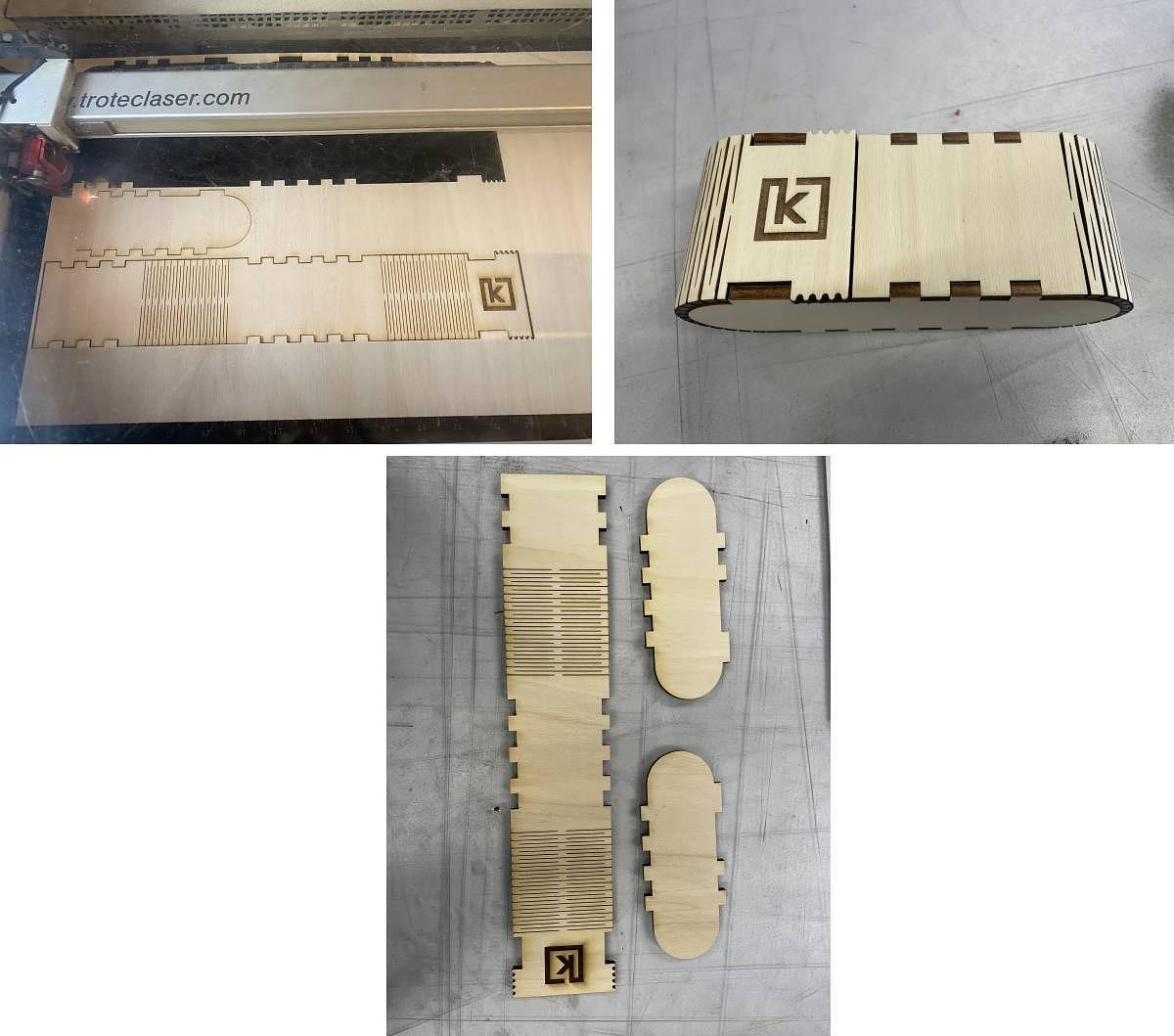
Nouvel étui : contreplaqué 5mm, nouveau modèle permettant une ouverture facilitée et logo déjà inséré.
L’étui nous satisfait au niveau de l’ouverture, mais paraît un peu gros. Malheureusement nous ne pouvons pas modifier la taille. Ce sera parfait comme ça. Une modification de l’orientation du logo et c’est parti pour une nouvelle découpe.
Après une étape de montage, l’étui circule de main en main et quelques critiques d’amélioration sont émises, notamment au niveau des bords noircis par la découpe laser : il est donc nécessaire de poncer l’étui. Une autre critique porte sur le fait que les lunettes n’ont pas de protection dans l’étui : il y a donc un risque de rayure des verres. Il est nécessaire de matelasser, ou en tout cas de garnir notre étui.
Nous nous rendons compte que le ponçage de l’étui monté abîme et raye les charnières. Il nous faut donc poncer avant d’assembler les différentes parties de l’étui.
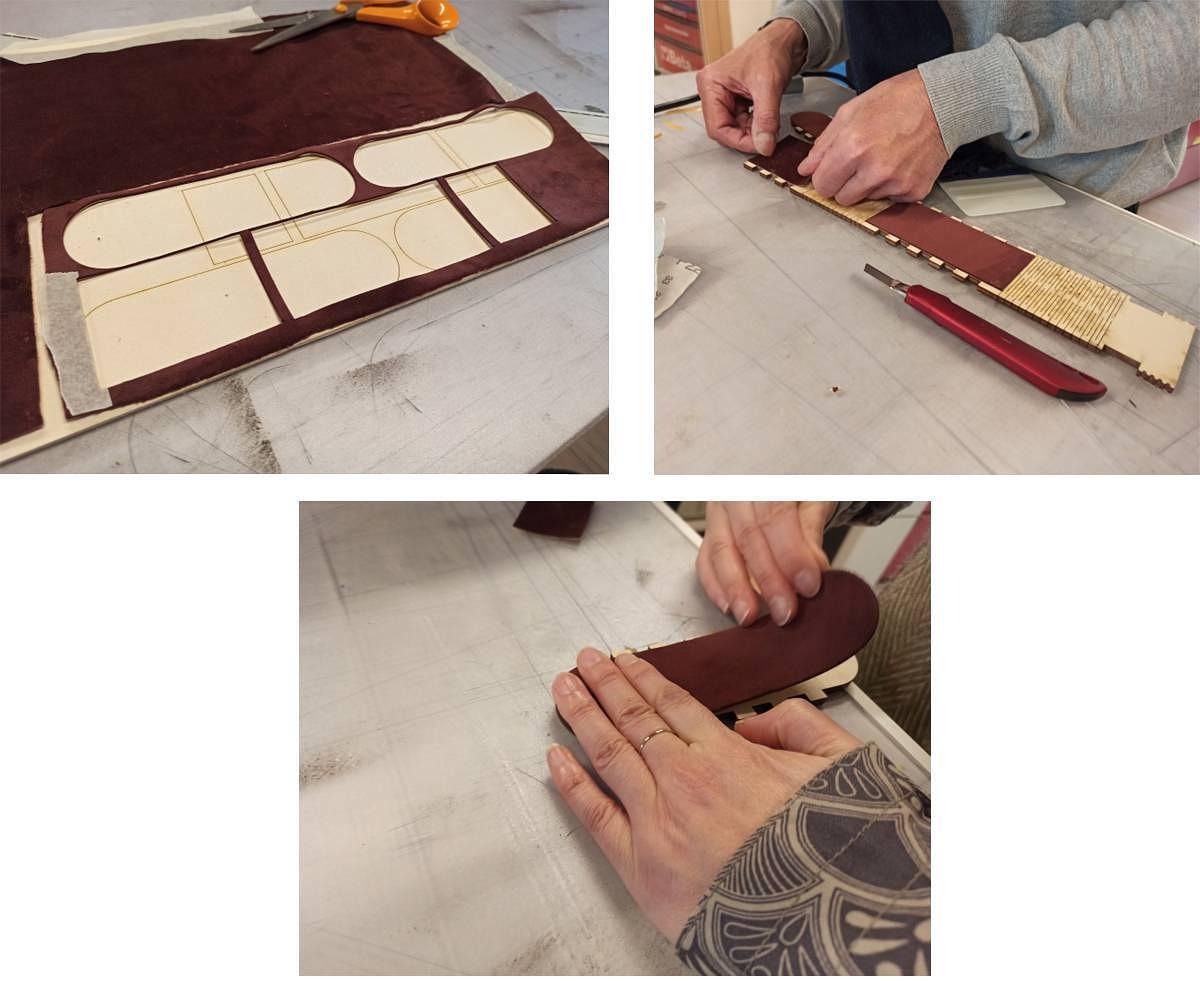
Nouvelle découpe du contreplaqué et nouveauté : nous avons trouvé un velours sur place qui fera parfaitement l’affaire pour notre étui. Nous découvrons alors la puissance de la découpeuse laser qui nous permet de ciseler au millimètre près le tissu aux dimensions de notre étui.
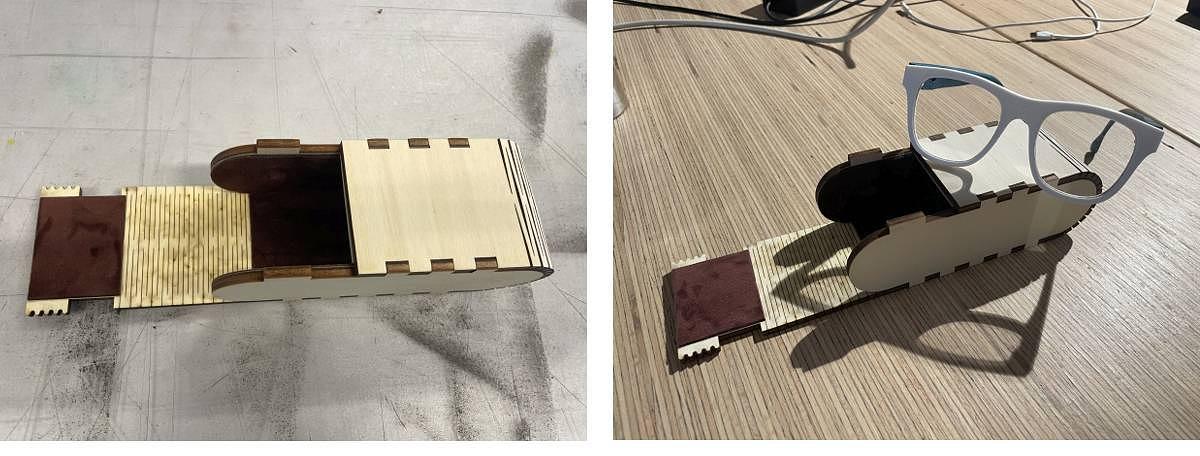
Nous ponçons et collons le velours avant l’assemblage de l’étui. Le résultat est à la hauteur de nos espérances. Nos montures ont enfin leur écrin.
LE PRESENTOIR
Pour valoriser nos montures, nous produisons également un présentoir en plexiglass à la découpeuse laser pour la touche finale. Notre projet est terminé !
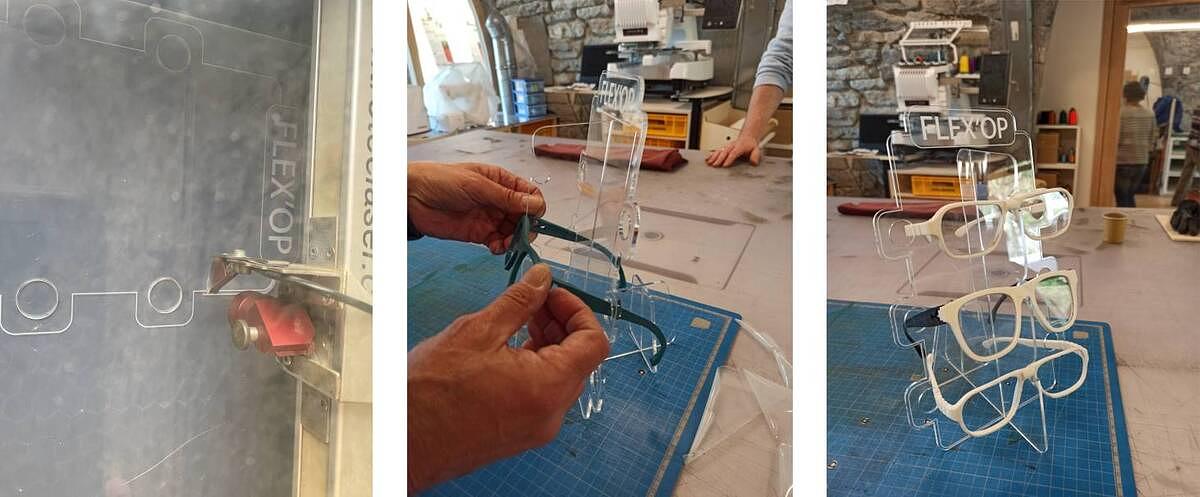
Ces trois matinées de fabrication au Fab Lab de la Casemate, encadrées par des formateurs bienveillants et à l’écoute, auront concrétisé cette aventure humaine dans le cadre du parcours de l’Arche aux innovateurs, et permis de mettre en avant cette expérience unique et riche en découvertes, en apprentissages et en échanges. Une belle semaine, remplie d’expérimentations, allant de satisfactions en déconvenues, mais avec toujours cette envie de nous améliorer et de donner le meilleur de nous-mêmes.
Entrer à la Casemate, découvrir le potentiel du Fab Lab, explorer le champ des possibles dans le cadre de ce parcours d’éco-innovation aura peut-être, qui sait, éveillé de nouvelles vocations ?
La porte de la Casemate se referme pour notre équipe, mais tous, nous repartons avec l'envie d'y revenir et de poursuivre cette belle aventure de créativité allant de l'idéation d'un projet, aussi minime soit-il, à sa concrétisation grâce aux rencontres et aux échanges uniques dans ce lieu particulier dédié à l’innovation.